Click on the images below to view full size.
Manufacturing Management System
Challenge
A manufacturer of child safety seats was beginning production on a brand-new seat model and required a software system to track and comply with very stringent safety regulations, allowing their product to be sold and distributed globally. Tracking accurate production data including precise variables like screw angle and torque was critically important in order to maintain Transport Canada and NTSB requirements. Verification was also required upon completing each stage of the production process: seat assembly, final packaging and product labelling.
Objectives
A securely structured database was required to accumulate and contain both production and packaging data. An interface also needed to be created for administrators in order to provide filtered reporting capabilities and product entries needed to be editable, as well as searchable by serial number. Error logging was another necessary feature in order to ensure a lower margin of error and maintain data integrity.
Results
CoreSolutions built an end-of-line application to scan and store packaging, shipping and regulatory documentation and to validate that correct materials have been included in the packaging. Simple and automated labeling reduced operator time and dramatically simplified processes. The system received data from a programmable logic controllers (PLC) and printed to a barcode printer. When anomalies were detected by the software, the system notified the operator, advising them of the error and allowing them to take the appropriate action, reducing defects.
Technologies
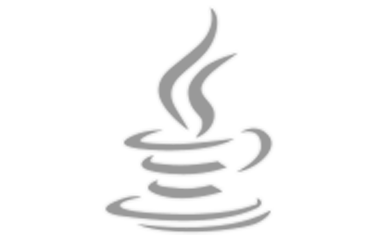
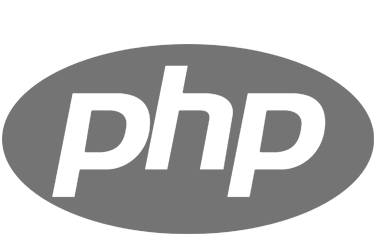
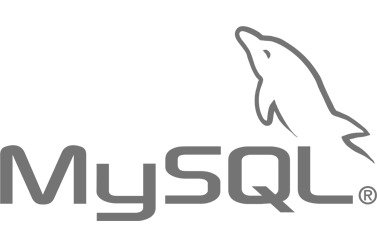
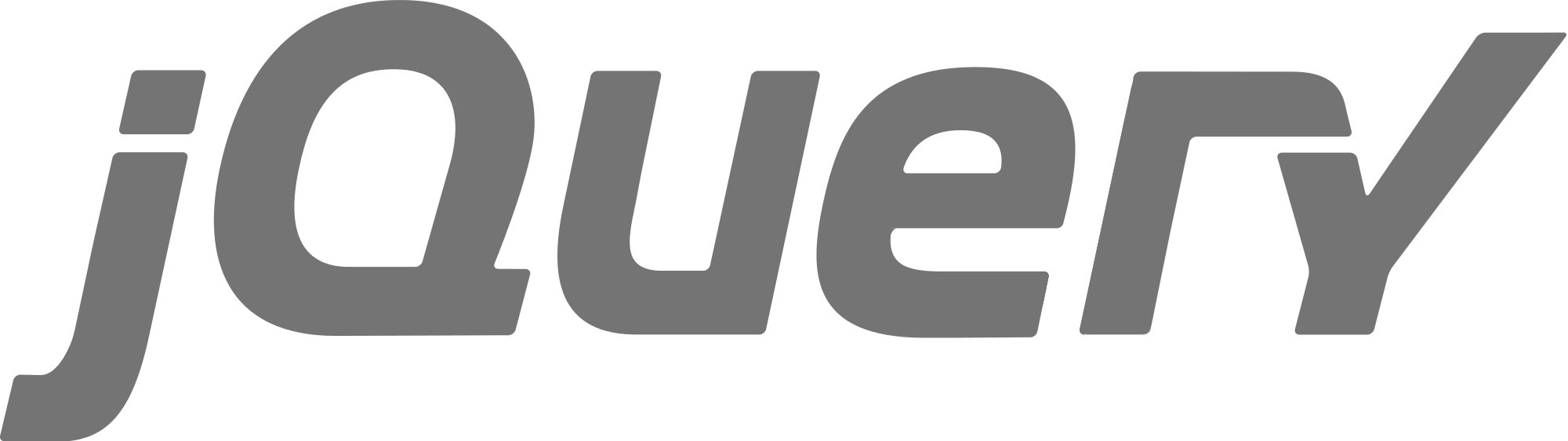
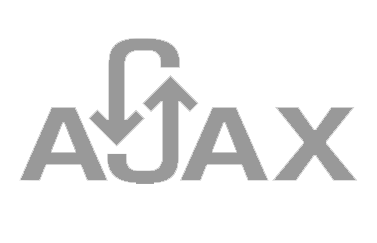
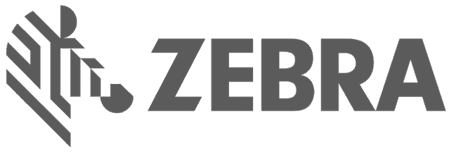