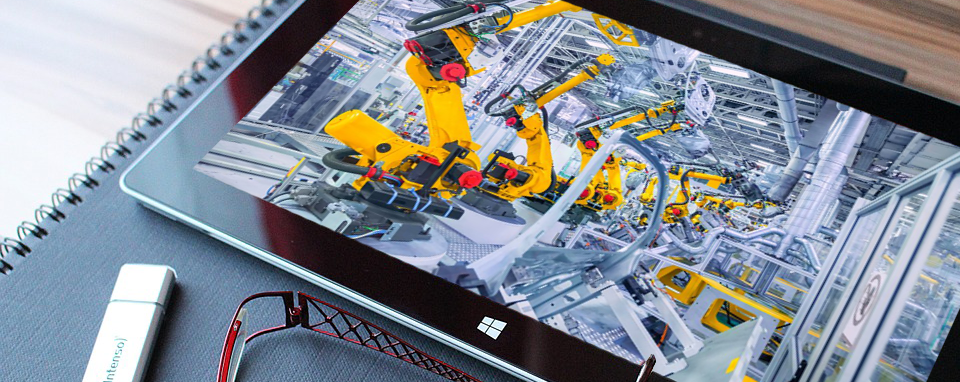
Manufacturing Database Redesign
Challenge
An established leader in the manufacturing industry with over 20 years of experience needed to update their legacy FileMaker system which no longer served their needs. Over time, the organization’s workflow had changed and the legacy system required manual data entry and duplicated effort. The organization had multiple methods for documenting required information including the system and paper forms. Government regulatory requirements stipulated that records needed to be kept for a number of years which created a lot of paperwork. When the government updated their required compliance forms, the existing forms were not setup to capture the required information.
Objectives
The client liked the FileMaker platform and wanted to update their system to match their existing workflow and be future proof for the next few years. The new system needed to be flexible in order to accommodate for changing government compliance regulations or workflow. The improved database needed to both decrease manual entry of data and improve accessing and storing work history.
Results
There was a lot of discussion regarding a full software rewrite, but we determined that we could achieve the majority of the system objectives through changes to the current system and adding the new workflow. While there would be some compromises in terms of the speed of the system, the modification ultimately led to the highest return on investment. Because most of their data now resided in a database, the client could effortlessly store and retrieve past compliance information instantaneously.
Technologies
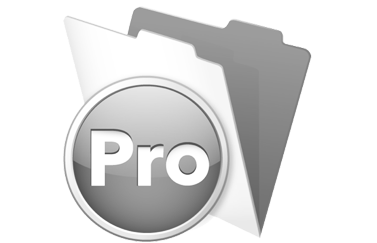
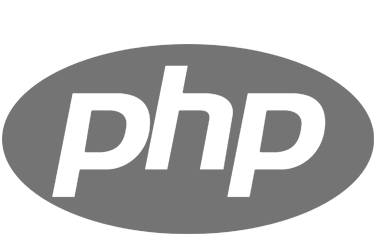
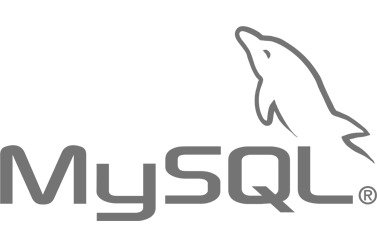
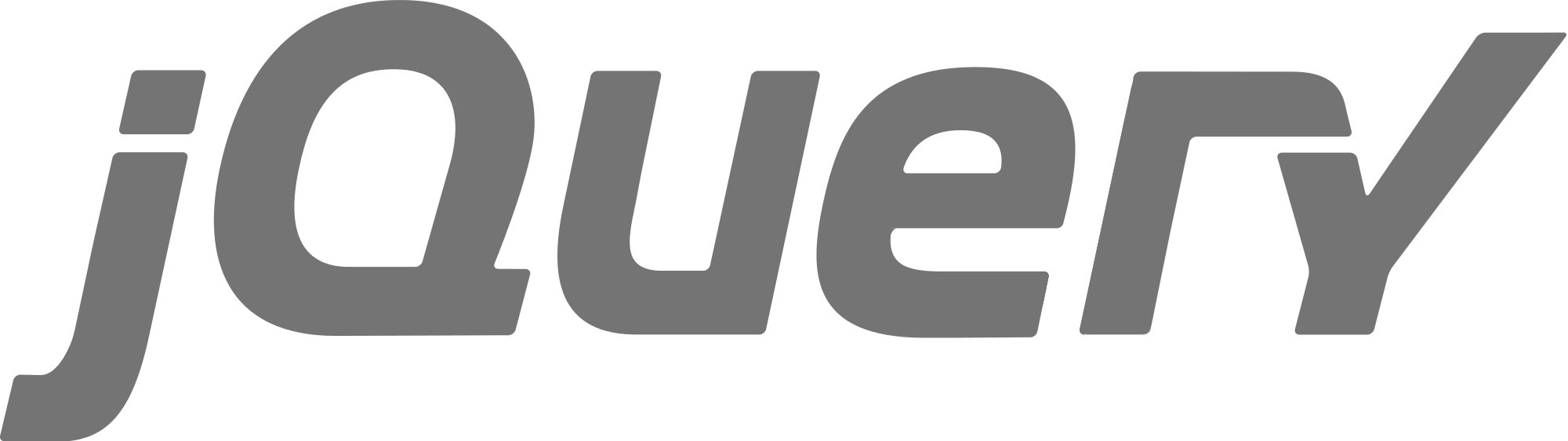